We hold ourselves to the highest standard
We make sure that everything we do aligns with the principles we hold dear.
Below are just a few of Brightstar’s key policies and principles. More information on each of these policies can be found in our code of conduct.
U-Tapao International Airport Fuel System
Ongoing
U-Tapao International Airport (UTP) is an airport located in Ban Chang District of Rayong Province, approximately 170 km from Bangkok. Originally serving as the Royal Thai Navy Airfield, UTP has experienced significant growth in commercial airline service in recent years. This growth highlights its potential as part of the Bangkok airport system, which includes Suvarnabhumi …
Our Sustainability Goals
June 2023
Brightstar is fully dedicated to achieving sustainability goals that prioritize the health of our planet. We recognize the importance of understanding and minimizing our environmental impact, which is why we conduct comprehensive environmental studies for every project we undertake. These studies allow us to assess potential risks and develop innovative solutions that align with our …
Nyaung-U (Bagan)
Ongoing
In 2019, Golden Myanmar Airlines (GMA) recieved permission from the Myanmar Investment Commission for the importation, storage distribution and dispensing of Jet Fuel to 7 regional airports around Myanmar. The first airport location to be developed is Nyaung-U, serving the ancient city of Bagan, a UNESCO World Heritage Site on the banks of the Irrawaddy …
Krabi International Airport: Hydrant Fuel System Project
August 2020
PTT have engaged Brightstar to prepare the FEED package for a new hydrant fuel system to be constructed at Krabi International Airport.
The FEED package includes a scope of work as the basis for EPC tendering.
Conceptual Study: Aviation Fuel Supply System for U-Tapao International Airport
November 2019
PTT engaged Brightstar to carry out the study and conceptual design of the aviation fuel supply and delivery systems required for the proposed development of U-Tapao Airport to become Bangkok’s third international airport.
The study encompassed three modes of supply (ship, pipeline and road tanker) upgrading of the existing fuel depot, new fuel hydrant and intoplane facilities.
Thomson Line Extension T316: Fuel Pipelines Tunneling Impact Assessment
Ongoing
Brightstar have been engaged by ARUP under a 2-year framework agreement to provide technical consultancy services relating to the impact of the Thomson-East Coast MRT Line, T5 extension, tunneling works on the existing fuel hydrant facilities at Changi Singapore Airport.
International Pipeline & Offshore Contractors Association (IPLOCA)
October 2019
The 53rd IPLOCA Convention was held in Bangkok from 30th September to 4th October 2019.
Brightstar participated in the convention and joined with PTT to deliver the opening technical presentation Key Success Factors for Pipeline Projects in Thailand.
Sihanoukville to Phnom Penh Oil Product Pipeline
April 2020
Kampuchea Tela Petroleum (Tela) engaged Brightstar in conjunction with our partners DRW, to provide Consultancy services for the proposed oil pipeline from Sihanoukville to Phnom Penh.
The 220km ‘multi-product’ pipeline will transport various white oil products from Tela’s existing marine import terminal at Sihanoukville to a new distribution depot in Phnom Penh.
This pipeline project and associated terminals will be the first oil pipeline project in Cambodia which will build energy supply security and contribute significantly to the country’s development.
U-Tapao International Airport Fuel System
Ongoing
Location
U-Tapao
Project Type
PMC
U-Tapao International Airport (UTP) is an airport located in Ban Chang District of Rayong Province, approximately 170 km from Bangkok. Originally serving as the Royal Thai Navy Airfield, UTP has experienced significant growth in commercial airline service in recent years. This growth highlights its potential as part of the Bangkok airport system, which includes Suvarnabhumi International Airport (BKK) and Don Meuang International Airport (DMK). The development of the new U-Tapao International Airport is a key component of the EEC development initiative, which consists of six major infrastructure projects.
The new UTP Airport will be developed and operated by U-Tapao International Aviation Co., Ltd. (UTA), a joint stock company formed by Bangkok Airways (BA), BTS Group Holdings (BTS), and Sino-Thai Engineering and Construction (STEC). The fuel system at the new UTP airport will be operated separately under a concession by Global Aero Associates Co., Ltd. (GAA), a joint venture between Bangkok Aviation Fuel Services (BAFS) and PTTOR. To ensure efficient project management, GAA has enlisted the services of Brightstar Engineering for project management consultancy (PMC), which includes various tasks such as project management support, fuel demand projection, and construction supervision consultancy.
The initial phase of the new U-Tapao International Airport’s fuel system comprises an airport depot and hydrant facilities designed to meet industry guidelines. The airport depot includes three Jet A-1 fuel vertical storage tanks, road tanker offloading bays, pipeline receiving facility, and various other facilities for fuel transfer and management. It also features a hydrant system with pumps, flushing and depressurization facilities, and emergency shutdown capabilities. Firefighting facilities and ancillary systems like drainage and utility systems are included as well. Additionally, the fuel hydrant system consists of twin 16″ hydrant feeder lines, hydrant loops covering different areas, and refueling points at aircraft parking stands. Sectional valve chambers, emergency fuel shut-off system, and monitoring instrumentation ensure safe and efficient fuel distribution.
The initial phase of the new U-Tapao International Airport’s fuel system comprises an airport depot and hydrant facilities designed to meet industry guidelines. The airport depot includes three Jet A-1 fuel vertical storage tanks, road tanker offloading bays, pipeline receiving facility, and various other facilities for fuel transfer and management. It also features a hydrant system with pumps, flushing and depressurization facilities, and emergency shutdown capabilities. Firefighting facilities and ancillary systems such as drainage and utility systems are included as well.
The fuel hydrant system consists of twin 16″ hydrant feeder lines, hydrant loops serving all aprons, and refueling points at aircraft parking stands. Sectional valve chambers, emergency fuel shut-off system, and monitoring instrumentation ensure safe and efficient fuel distribution.
Overall, the development of U-Tapao International Airport and its fuel system signifies its potential for growth within the Bangkok airport system. The involvement of multiple companies and the implementation of industry guidelines highlight the commitment to quality and efficiency in the airport’s operations.
Brightstar Engineering, while providing project management consultancy for the U-Tapao International Airport’s fuel system, is fully dedicated to applying sustainability goals and minimizing environmental impact. The company commissions comprehensive environmental studies, actively promotes sustainable jet fuels, and promotes carbon net-zero by 2050. With a commitment to making a positive impact on the environment, Brightstar aligns the project with its sustainability objectives, contributing to a greener and more climate-accountable aviation industry.

Our Sustainability Goals
June 2023
Brightstar is fully dedicated to achieving sustainability goals that prioritize the health of our planet. We recognize the importance of understanding and minimizing our environmental impact, which is why we conduct comprehensive environmental studies for every project we undertake. These studies allow us to assess potential risks and develop innovative solutions that align with our sustainability objectives. Additionally, we are actively engaged in researching and promoting sustainable jet fuels, recognizing the aviation industry’s contribution to carbon emissions. By exploring alternative fuel sources, we aim to reduce our carbon footprint and contribute to a greener future for air travel. As part of our commitment, we have set a non negotiable target to achieve carbon net-zero by 2050. Brightstar is resolute in its dedication to sustainable practices and remains committed to making a positive impact on the environment at every opportunity.
Nyaung-U (Bagan)
Ongoing
In 2019, Golden Myanmar Airlines (GMA) recieved permission from the Myanmar Investment Commission for the importation, storage distribution and dispensing of Jet Fuel to 7 regional airports around Myanmar.
The first airport location to be developed is Nyaung-U, serving the ancient city of Bagan, a UNESCO World Heritage Site on the banks of the Irrawaddy river in the central plains of Myanmar. The airport is earmarked to receive direct international flights and the installation of a modern Jet fuel supply system has therefore been prioritised.
Brightstar provided the desgn to GMA’s EPC Contractor for a completely new green field fuel depot, located adjacent to the airport.
The facility was designed to be ‘fit for purpose’ and fully compliant with the requirements of international standards, ie. EI (Energy Institute) and JIG (Joint Inspection Group).
Given the relative remoteness of the location and the potential replication at multiple other locations, a modular design was adopted for the key components, including:
- 3 No. above ground 20 foot ‘containerised’ UL 142 self-bunded (dual wall) stainless steel storage tanks
- Automatic Tank Gauging system with remote monitoring capability
- Road tanker unloading / refueler loading skid with common pump, filter, metering and intergral refueler test facility as per JIG4 requirements
- Centralised tank fast flush and sampling unit
- Proprietary full retention (forecourt type) Oil Separator
In addition, the following facilities were provided:
- Firefighting system with storage tank, fixed monitors and portable foam unit
- Unloading/loading Shelter and access gantry
- Office building, control room and laboratory
- Site access roads, drainage and security fencing
The design reflected EI and NFPA safety distances and included provision for expansion of the storage capacity (additional tanks) and the addition of future maintenance workshop.
Krabi International Airport: Hydrant Fuel System Project
August 2020
Client
PTT Public Co., Ltd.
Location
Krabi, Thailand
Project Type
FEED Design
Krabi International Airport (KBV) has embarked on an expansion to build a third terminal and extend the aircraft parking aprons and associated infrastructure to increase capacity to 8 million passengers per year.
Construction of the new terminal is ongoing and installation of the new apron pavement is substantially completed.
The total number of aircraft stands will be increased to 20, 14 of which will be multiple parking type capable of accommodating one large (‘Code D/E’) or two smaller (‘Code C’) aircraft.
The current Airport Fuel Depot supplies approximately 60 million litres of jet fuel per year. The fuel is imported by dedicated bridger tankers from PTT Surat Thani fuel depot and delivered to the aircraft by refueller vehicles of 25,000 and 50,000 litres capacity.
Krabi has seen a rapid growth in medium and long haul flights, in particular from Europe, serviced by large (Code E) Aircraft such as Airbus A350 and Boeing 787 Dreamliner aircraft, which require high volume fuel uplifts of 100,000 litres or more.
The current truck based aircraft refueling operations present a limitation in terms of refueling rates, which may impact on aircraft turn-round-times as the air traffic volumes increase further.
PTT have therefore decided to improve overall fueling efficiency by installation of a fuel hydrant system which will enable much higher fueling rates and remove the need for multiple refueller deliveries for the larger aircraft.
The existing fuel depot will also be expanded and upgraded to supply the fuel hydrant and the increasing fuel demand at the airport.
Brightstar Scope of Work:
The work comprised:
- Review and develop the hydrant design concept
- Compile fuel demand design basis
- Carry out hydraulic calculations to verify hydrant and feeder line sizing
- Review aircraft stand parking positions and verify hydrant fuel point locations
- Develop the FEED Design package for the new Hydrant Fuel System
- Review the existing fuel depot facilities (including ongoing work packages) and identify any modifications and additions required to support the new hydrant fuel system.
- Prepare the scope of works as the basis for tendering and execution of an EPC contract for the hydrant construction and depot modifications.
- Detailed cost estimate for the works
- Prepare preliminary construction method statements for key activities:
- HDD hydrant installation
- Hydrant riser and pit box installation
- Assist PTT in presentations to the Department of Airports in support of their application for a project construction permit
Site visits were carried out to assess the existing depot facilities, ongoing expansion works and to survey the hydrant and feeder line routes and construction methodology.
Value Added:
Hydrant Configuration
A twin parallel 10 inch hydrant configuration was adopted to enable redundancy in operation and flushing capability to maintain fuel cleanliness at the highest standard.
Section valves were installed in chambers to allow isolation of individual sections for maintenance and inspection purposes without disconnecting flow to other sections. The system sizing allowed these valves to be manually operable only, removing the need for power supplies and remote actuation facilities in the valve chambers and reducing cost accordingly, without in any way compromising the safety or operability of the hydrant fuel system.
Operation and Emergency Shutdown of the hydrant system is performed by equipment and control systems located in the airport fuel depot; the only apron side facilities required were the emergency fuel shut off units installed at each aircraft stand, cabling to a marshalling cabinet installed in the Airfield Lighting Room and communications equipment to send the signals by dual redundant fibre optic cables to the fuel depot.
Hydrant Sizing
Detailed passenger throughput forecasts were not available so Brightstar applied ‘reverse’ sizing principles to model hydrant hydraulics. This involved using typical stand utilsation factors, likely apron distribution and aircraft turn round times (TRT) to estimate the peak fuel uplift. This was then input to a preliminary hydraulic model to confirm optimal pipe sizing.
Hydrant Alignment
Based on experience from other airports and fuel dispenser operational limitations, Brightstar were able to locate the hydrant lines and all required refueling pits within a straight 4.5 meter corridor along the length of the apron.
This minimized the cost – and disruption – of installing the hydrant pits in the existing apron.
Hydrant Construction
At the time Brightstar were appointed, the construction of the new aprons was substantially complete. Therefore, to minimize the need for intervention in the apron areas, Brightstar developed a methodology for construction of the hydrant beneath aprons by Horizontal Directional Drilling (HDD) technique, using a highly accurate guidance system.
A ‘J-profile’ HDD was adopted in order to maintain the required slope on the finished hydrant, minimize the number of drills required and the depth of the hydrant, in order to facilitate post-drilling the connection of the hydrant risers and pit boxes.
The proposed HDD design also allowed the number of sectioning valve chambers to be reduced to just 3, of which only the central chamber was required to be installed beneath aircraft load bearing apron pavement.
Calculations were also performed to model the ground reaction to the drilling operation beneath the apron; based on this calculation, it was determined that no post-drill grouting or polymer treatment of the soil was required to support the subgrade and apron above.
These engineering measures yielded construction cost savings of around 20%, enabling the project to be delivered within the available budget.
Hydrant Pit Installation
Installing the Hydrant pits and 6 inch riser pipes to the hydrant pipes after HDD was identified as a critical activity to the success of he project.
Brightstar therefore developed a detailed methodology for installation of the risers and pits which the selected EPC Contractor will be required to adopt.
The methodology addresses all the key requirements including:
- Minimise the required area of apron pavement removal
- Safety and fresh air supply in excavated access shaft
- Avoidance of disturbance to the surrounding subgrade
- Field adjustments to the hydrant pit box position and elevation with respect to the surrounding apron finish level.
- Compaction levels for backfill in excess of the requirements from the apron pavement design for subgrade compaction.
Feeder Line Routing
The original concept had been to feed the hydrant by a feed from the depot joining the hydrant at a point part way along the apron.
This would have entailed removal of a large section of newly installed apron to install the connection and the installation of an additional valve chamber in the apron.
To avoid this, Brightstar revised the routing of the feeder lines to connect to the end of the hydrant away from the apron.
This meant that the feeder lines could be installed mostly by open cut construction and no apron removal will be required, minimizing project costs and risks accordingly.
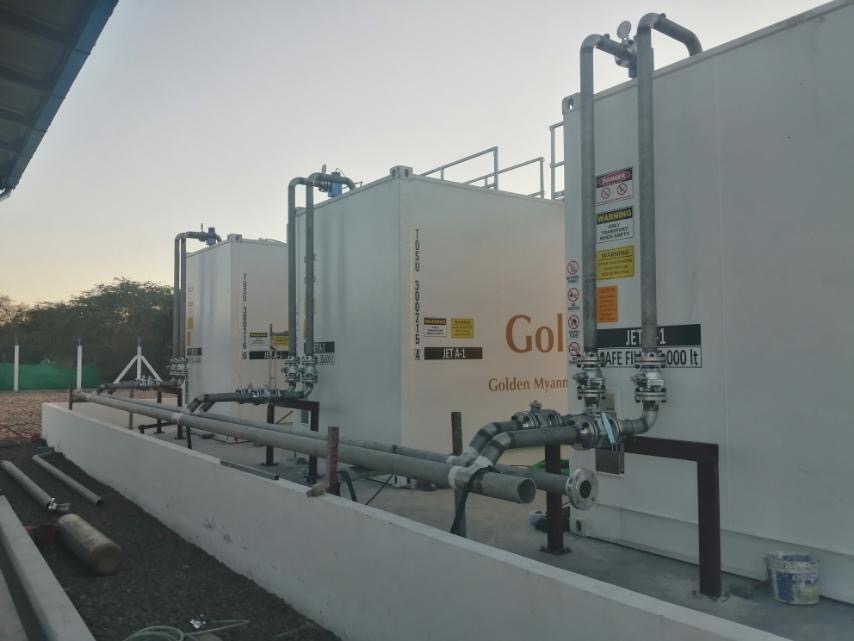
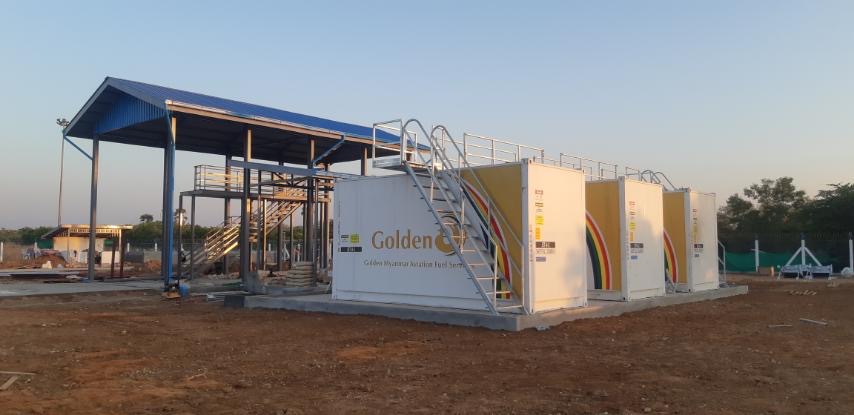
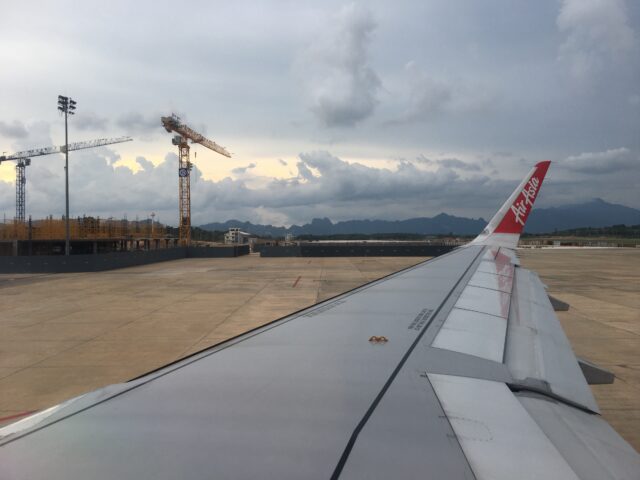
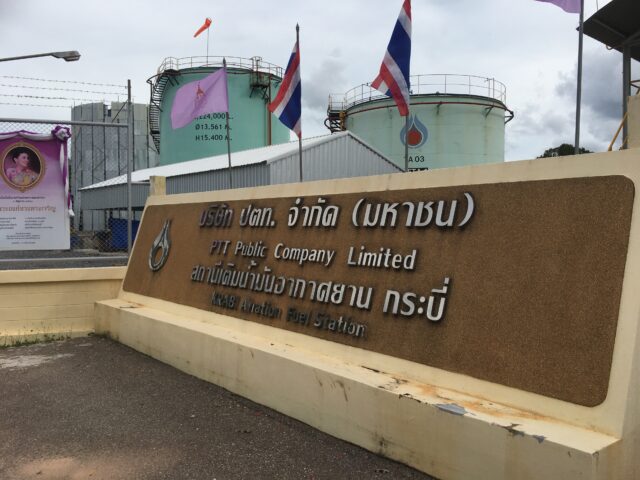
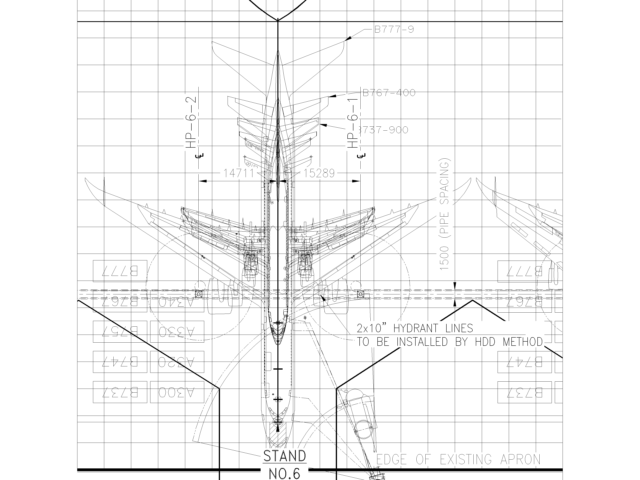
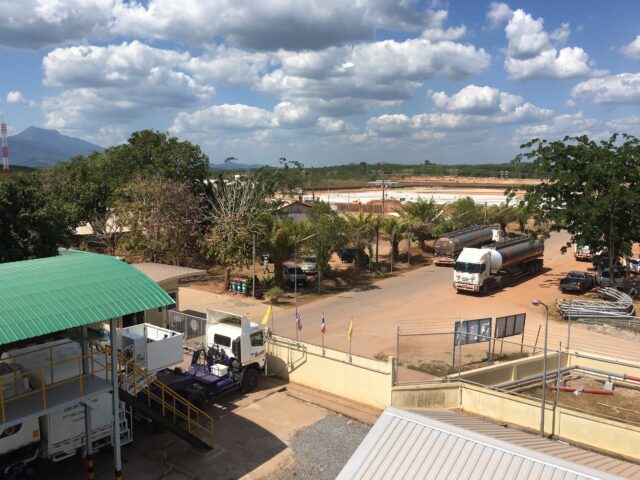
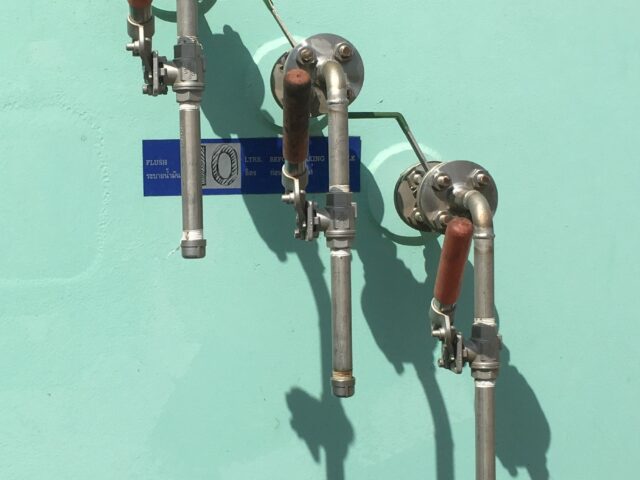
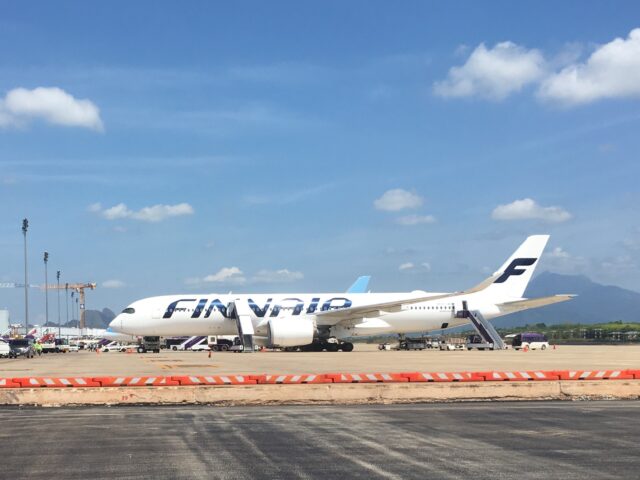
Conceptual Study: Aviation Fuel Supply System for U-Tapao International Airport
November 2019
Client
PTT Public Co., Ltd.
Location
Rayong, Thailand
Project Type
Study
The Government of Thailand plans to develop U-Tapao Airport as the third international airport serving Bangkok and the Eastern Seaboard, as part of the ‘Eastern Economic Corridor’ (EEC) initiative.
The development comprises new Passenger Terminals, Cargo, Maintenance, Repair & Overhaul (MRO) facilities, Aviation Training Centre and a Free Trade Zone to serve the ‘S-Curve’ industries targeted as part of the EEC development.
The initial airport capacity will be 12 million annual passengers in the initial phase increasing to an ultimate capacity of 60 million.
PTT is the aviation fuel provider at the current airport and intends to tender for the upgrading and expansion of the aviation fuel supply facilities to serve the new airport development.
PTT appointed Brightstar to study the fuel system required to support the airport development, which was divided into 4 separate elements (sub-projects):
-
- Airport Fuel Hydrant System (including Intoplane facilities)
- Upgrading of the existing Fuel Depot
- Marine Tanker jetty unloading and transfer facilities
- Dedicated Fuel pipeline from Map Ta Phut refineries
Brightstar Scope of Work:
In order to estimate the required capacity of the fuel supply system, Brightstar carried out fuel uplift projections for the initial, intermediate and ultimate phases of the airport development.
Based on these projections and the available data for the airport configuration, Brightstar carried out an assessment of each element of the system which considered the options, utilization of existing facilities where appropriate and order of magnitude costs. Recommended configurations were presented and iterated with PTT.
Following agreement, Brightstar developed conceptual designs and associated cost estimates for each element of the system.
Value Added:
Fuel Uplift Projections
Fuel uplifts are often calculated by simple extrapolation of historic volumes and/or the application of typical demands to projected passenger or ATM numbers. However, this methodology does not deliver confidence levels concomitant with multi-million-dollar investment decisions.
Brightstar adopts a more sophisticated approach to fuel uplift projection which reflects the complex array of influences including aircraft mix, journey profile and industry trends.
For this project, the projections were based on the various passenger and air traffic movement (ATM) forecast data sets published by the Government as part of their market soundings, historic fuel data for the existing Bangkok airports and typical fuel uplift data published by IATA and others.
Using our accumulated knowledge base from other airport developments, Brightstar then processed this data for the assessed aircraft mix, anticipated route network and allowances for load factor, fuel efficiencies, etc.
This provided the basis for the sizing of the various supply facilities including jetty, pipeline and along with an assessment of strategic stock holding requirements, for the fuel storage capacity at the depot.
For sizing the hydrant fuel system, the maximum instantaneous fuel demand was required. Peak hour departing ATM forecasts were used as the basis for this and applied for the sizing of the buried pipe network and pump station capacity.
The resulting fuel uplift projections produced by Brightstar provided a robust basis for the optimal sizing and configuration of the various system facilities and in turn an accurate assessment of project costs for financial analysis and project investment appraisal.
Master Plan
The Master Plan had not been finalised at the time of the Study. Two very different basic airport terminal configurations were under consideration by each of the prospective concessionaires.
Brightstar therefore prepared apron stand layouts and conceptual fuel hydrant Designs for both potential options, allowing the study to be completed and arming PTT with the information to evaluate and respond quickly and definitively to the requirements of either selected airport concessionaire.
Fuel Depot Upgrade
The existing fuel farm was originally constructed to US military standards with large tank spacing. This led to a number of unusual technical challenges including pump suction head, fire protection requirements and power supplies for the added facilities.
Brightstar were able to develop cost effective solutions to all these challenges which were incorporated into the conceptual design for the fuel depot upgrade and cost estimate.
Landside Operating Base
Due to the diverse fuel supply facilities requiring control, the mixed use configuration of the existing fuel depot and its distance from the airport apron areas, Brightstar devised the concept of a Landside Operating Base (LOB) as a common facility to provide integrated control, operations and maintenance facilities for the various supply elements. The LOB also includes testing, maintenance and calibration facilities for the Fuel hydrant dispenser and refueler vehicles, separately from the airside GSE staging facilities provided for in the airport master plan.
The LOB concept will allow PTT to implement the fuel system projects with a lower dependency on the readiness of airport provided infrastructure than would otherwise be the case.
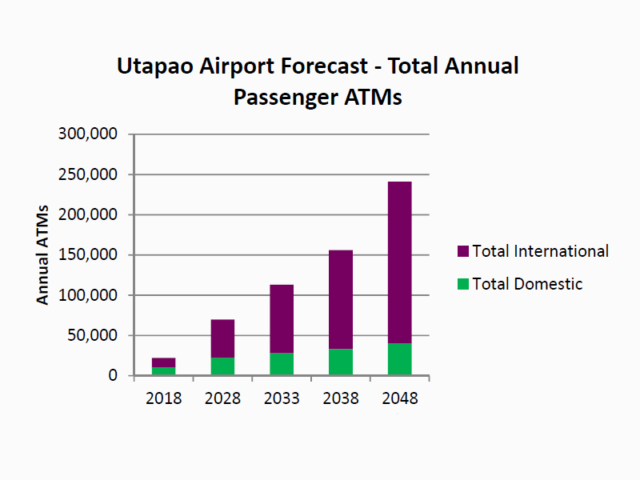
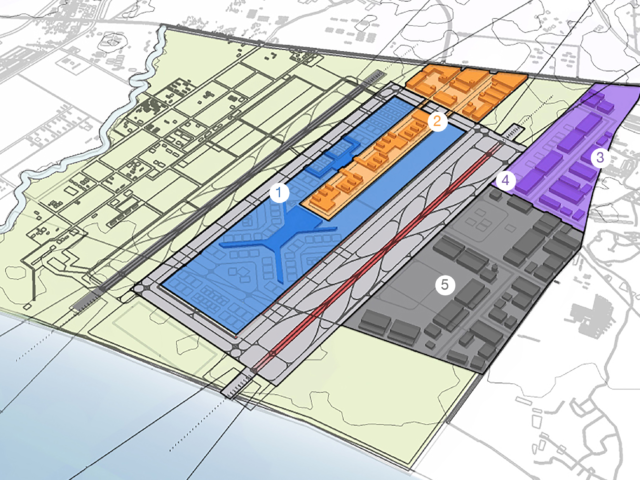
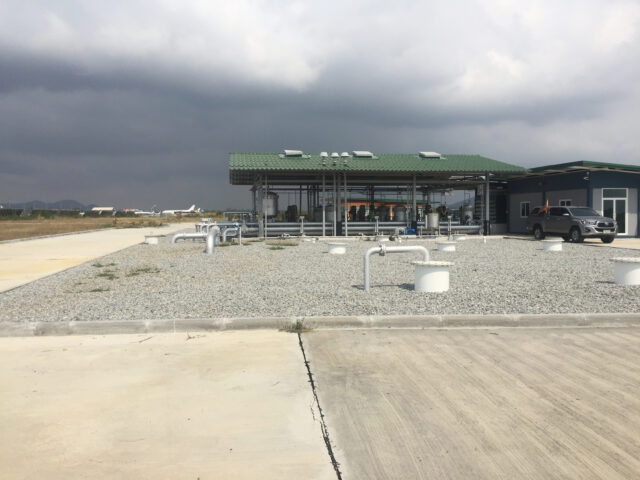
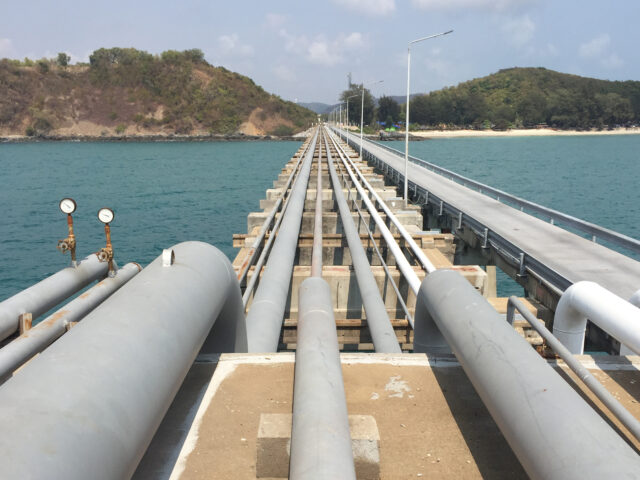
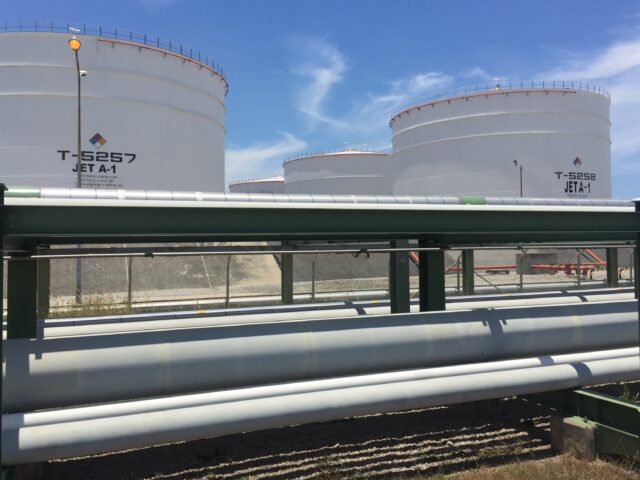
Thomson Line Extension T316: Fuel Pipelines Tunneling Impact Assessment
Ongoing
Client
ARUP
Location
Singapore
Project Type
Technical Consultancy
The Singapore Changi Airport Terminal 5 development will add 50 million passengers per year capacity, bringing the total across all terminals to 140 million from the current 85 million.
To serve the expanded airport, the Thomson-East Coast Line will be extended from Sungei Bedok to Changi Airport station, connecting the new Changi Airport Terminal 5 with the existing Terminals 1-3 at the existing Changi Airport station. The Changi Airport branch of the East-West Line from Changi Airport to Tanah Merah will also ultimately be converted to the Thomson-East Coast Line system.
Contract T316 has been awarded to Shanghai Tunnel Engineering Co. (STEC) covering the construction of twin bored tunnels from T5 development towards Changi Airport (CGA) T2 Station North Finger Pier. STEC have engaged ARUP as their design consultant for the contract.
These tunnels will pass beneath the existing airport terminals and aprons in a number of locations. Changi Airport Fuel Hydrant Installation Pte Ltd. (CAFHI) the operator of the fuel hydrant system at the airport, are concerned that appropriate measures are taken to avoid or mitigate any impact the tunneling works may have on the buried fuel hydrant pipelines at these crossing locations and it is a requirement of the contract that an approved aviation specialist company be appointed to ensure that such measures are implemented.
Brightstar Scope of Work:
As one of CAFHI’s approved aviation fuel specialists, Brightstar were appointed by ARUP to provide technical advice and support for the design and construction of the tunnels.
Brightstar’s scope includes the review of STEC’s consultant’s tunneling model to assess the impact on the buried hydrant fuel lines in terms of the allowable stresses due to imposed deflections as well as the maintenance of an acceptable pipe profile as required by the JIG and EI standards.
Brightstar’s scope also includes the recommendation of appropriate inspection techniques to accurately locate and assess the condition of the buried lines, review of the proposed construction methodologies, representation at meetings and workshops and attendance on site during the critical construction periods.
Value Added:
As one of the world’s busiest airports, access for pre-installation investigation works is severely limited and all construction works subject to rigorous planning, review and risk assessment processes.
Brightstar’s unique combination of aviation fuel systems and oil pipeline design and construction expertise has enabled us to provide robust advice based on proven methodologies and techniques which delivers the project stakeholders the high level of confidence they require to sanction the works.
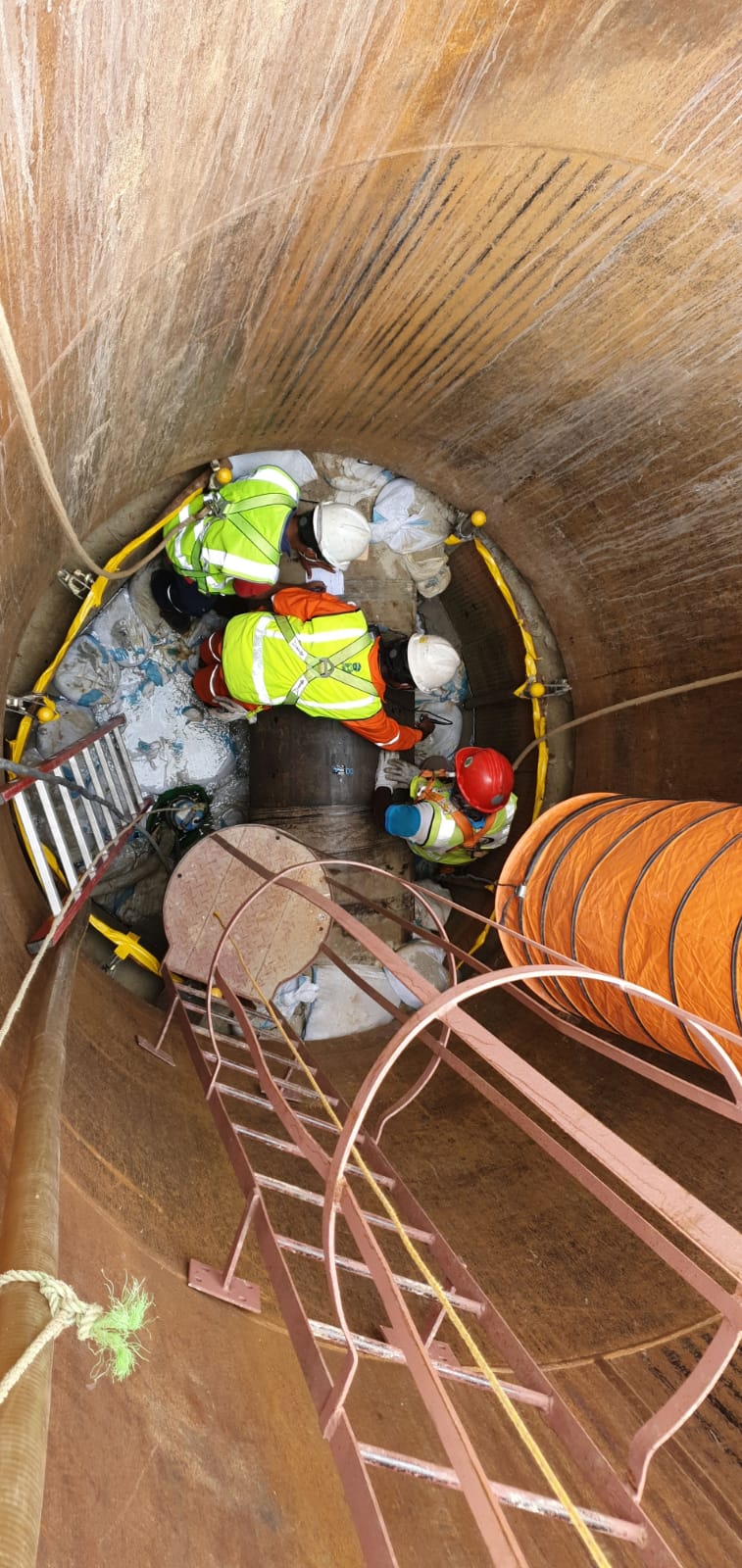
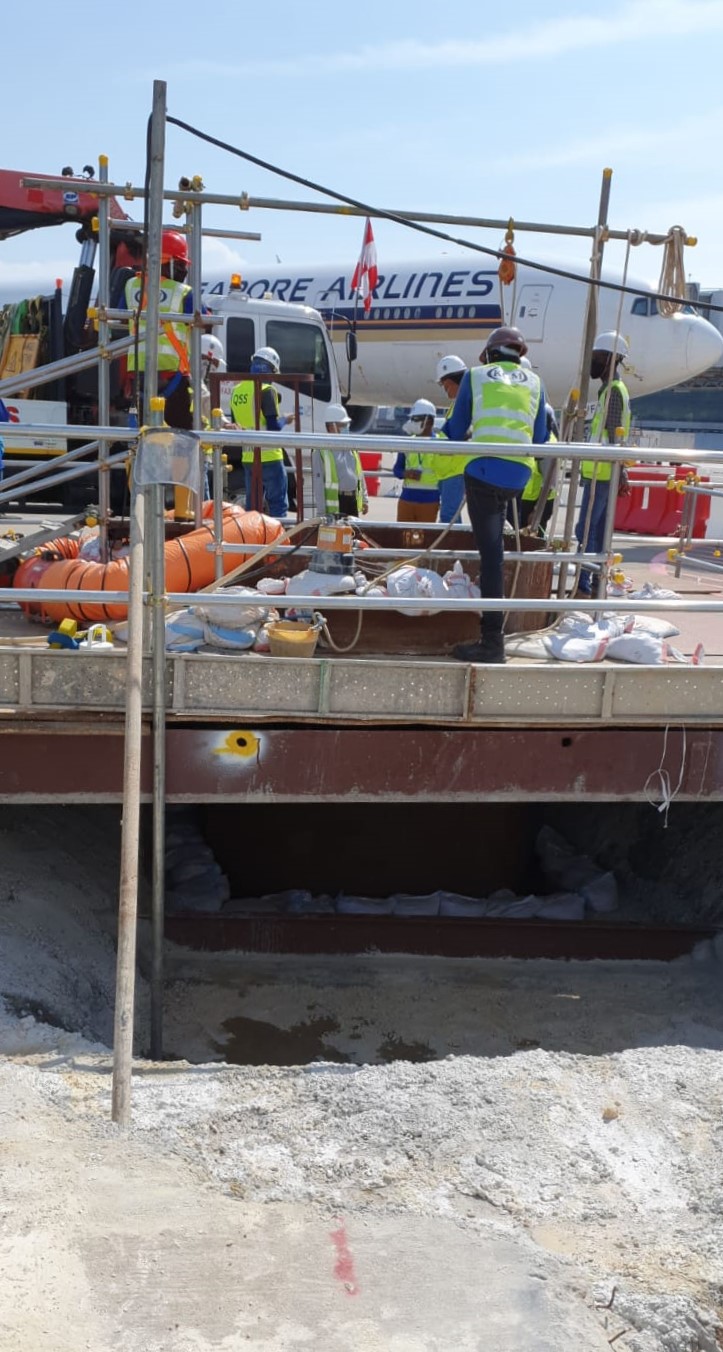
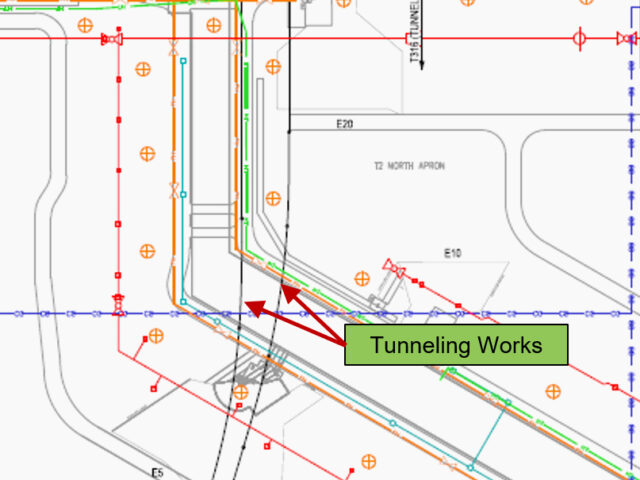
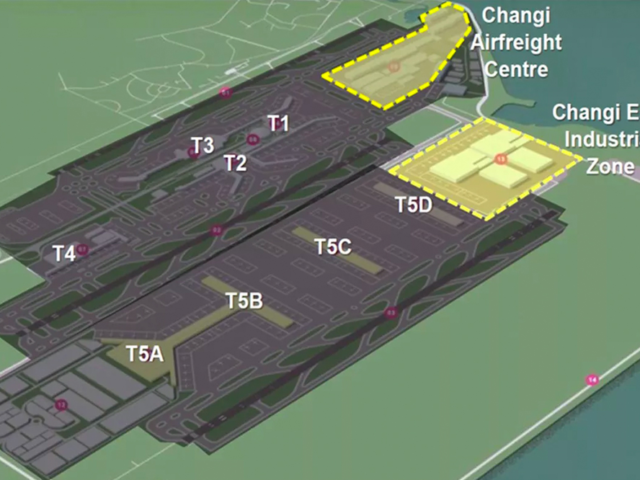

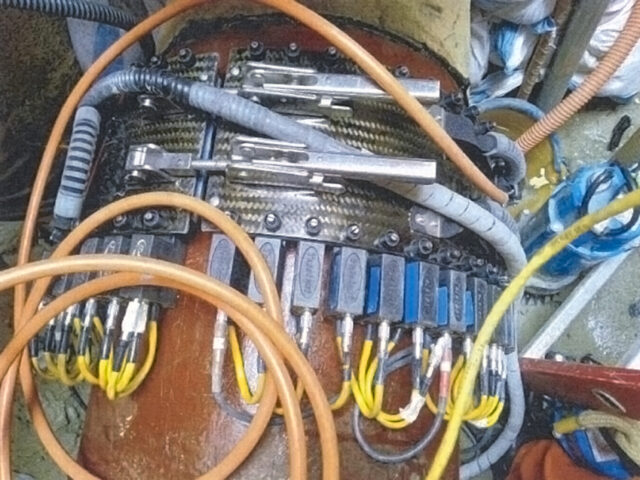

International Pipeline & Offshore Contractors Association (IPLOCA)
October 2019
Event
IPLOCA 53rd Annual Convention
Location
Bangkok, Thailand
The IPLOCA Convention is an annual gathering of leaders in the pipeline industry. It is attended by its Regular and Associate Members as well as Corresponding, Academic and Honorary Members, Media Partners, guests and accompanying spouses.
The five-day event includes a series of technical sessions, meetings, social events and tours. In an informal setting, senior executives from the pipeline industry are able to have an update on the current status of the industry whilst building relationships, networking, sharing ideas and holding business meetings with their peers from all over the world.
At the General Meetings, high profile speakers deliver presentations which focus on projects being developed, shared experiences of projects undertaken, future major projects and risk analysis.
IPLOCA awards are also presented at the Convention to recognise the most significant achievements and contributions of members to the pipeline industry.
Brightstar Activities:
Brightstar Managing Director Robert Avery, in conjunction with a senior representative from PTT, Thailand’s major oil & gas company, delivered the opening technical presentation to the General Meeting, entitled Key Success Factors for Pipeline Projects in Thailand.
The presentation included a regional look ahead for major pipeline projects and can be accessed at the IPLOCA website here (https://www.iploca.com/platform/content/element/30956/1.Avery-Yimsakul.pdf)
Brightstar also hosted a Business to Business (B2B) session at which meetings were held with several leading international and regional pipeline engineering and construction companies including, Bechtel, CCC, McConnell Dowell, Murphy, Nacap, PEAL, SICIM and Spiecapag.
Sihanoukville to Phnom Penh Oil Product Pipeline
April 2020
Client
Kampuchea Tela Petroleum
Location
Cambodia
Project Type
Owner Engineer / Consultant
Currently, Tela imports various oil products by marine tanker to their terminal at Sihanoukville port in the south of Cambodia. From there, the products are transported by road tanker to fuel stations around the country. This includes approximately 130 road tanker journeys every day between Sihanoukville and Phnom Penh.
To reduce the environmental impact of the road tankers, optimize long term operational costs and enhance supply security, Tela propose to construct an oil pipeline to transport Diesel, Gasoline and Kerosene products between Sihanoukville and a new distribution depot under construction on the outskirts of Phnom Penh.
Offtakes from the pipeline are also planned to supply intermediate depots in the future.
Tela has engaged a FEED contractor to carry out the basic design of the proposed multi-product oil pipeline and facilities comprising:
- 220 km pipeline
- Initial Pump Station and pipeline dispatch facilities at Sihanoukville Terminal
- Intermediate Block Valves
- Intermediate Pump Station (future)
- Pipeline Receipt Facilities at Phnom Penh Depot
The FEED and related cost estimate will be used in establishing whether the project meets the required financial investment threshold to proceed.
Brightstar Scope of Work:
Tela appointed Brightstar, in conjunction with our partners DRW, to provide Owner Engineer services during the FEED, including:
- Representation of Tela at Kick off and Progress meetings
- Pipeline route selection
- Review and approve FEED Contractor’s design submissions
- Represent Tela at formal Design Reviews
- Represent Tela at project HAZOP
- Project management and progress reporting
In addition to the above, Brightstar is providing advice on project definition, tendering and implementation strategies for Tela.
Value Added:
As the first long distance pipeline in Cambodia, this project has presented a number of challenges which Brightstar’s engineering team have been able to address.
Project Optimisation
At the project outset, Brightstar worked closely with Tela to ensure the project objectives and requirements were clearly defined and understood.
The project was to adopt a value approach to avoid over-engineering and unnecessary cost escalation which are too often features of emerging market projects..
This approach was carried forward into the design brief provided to the FEED Contractor and was applied during design development.
The result is a project which has been optimized to deliver Tela’s objectives in the most cost effective way. Particular aspects subjected to optimization include:
- Pipe diameter vs operating pressure
- Pipe material vs. wall thickness
- Addition of future intermediate pump stations to minimize initial capex and achieve phased throughput increases
- Flowrate vs. interface generation
- Consideration of flow enhancing additives for additional future capacity increases
Community Relations
It is to be expected that the project will encounter a level of apprehension and perhaps resistance, during construction, from the public who are not familiar with pipeline construction.
At this design stage, the pipeline route and the proposed construction methodologies have therefore been selected to minimize the impact on communities wherever possible.
In advance of construction public participation and information campaigns will be implemented to explain the project, its benefits and to address the concerns of the communities.
Constructability
The pipeline route includes some challenging areas for construction including limited access, congested road intersections, swampy areas, river crossings, etc.
Considering that specialist pipeline construction equipment and operators will need to be imported, Brightstar has placed particular emphasis on ensuring the proposed construction methodologies make effective use of imported machinery and maximise use of locally available equipment and skill levels.
Security
The security of the pipeline and protection from attempted fuel theft are especially important in locations such as this; Brightstar’s engineering team has ensured that an effective pipeline leak detection system has been specified, suitable for the location and environment, which will support the operational campaigns and pipeline patrols in identifying any attempt to tap into the pipeline and to avoid the disastrous consequences that can result from such illegal activities.
Batch Tracking
In operating a multi-product pipeline, the need to plan and develop an effective batch cycle is critical, as is the monitoring of the cycle and the progress of the product batches through the pipeline, to ensure that switching of receipt tanks is performed effectively and to minimize the volume of interface (‘transmix’) generated in the pipeline, which must be reinjected within tight product contamination limits.
As this will be the first pipeline to be operated by Tela, Brightstar have ensured that a proprietary batch tracking system is included in the scope of the contract to enable Tela’s operations team to effectively manage the pipeline inventory and batch cycle from the commencement of pipeline operations.
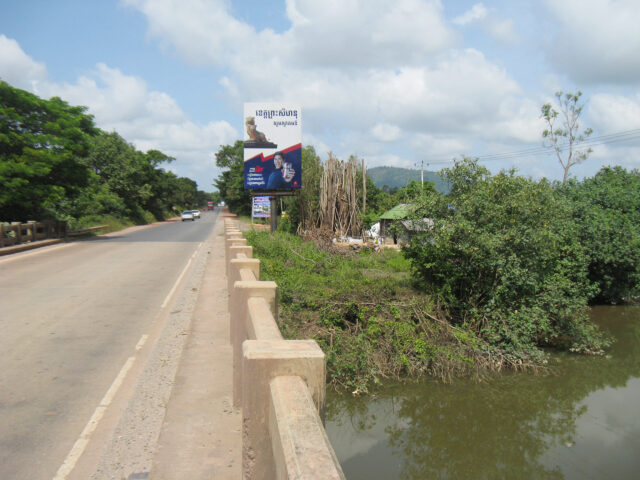
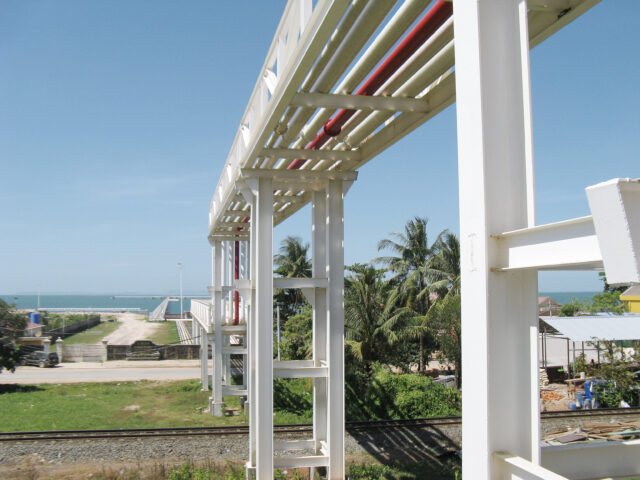
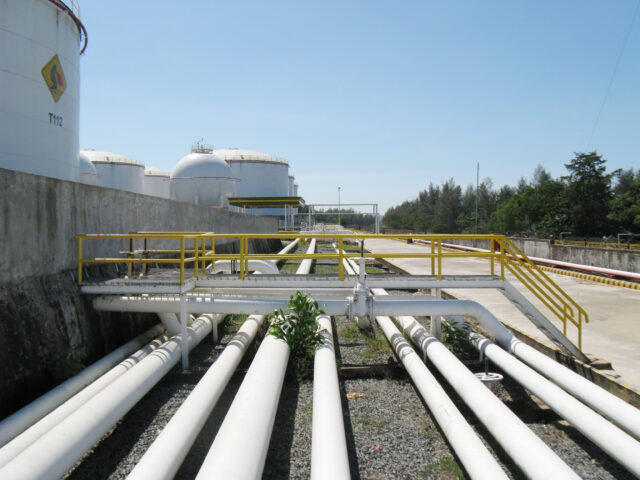
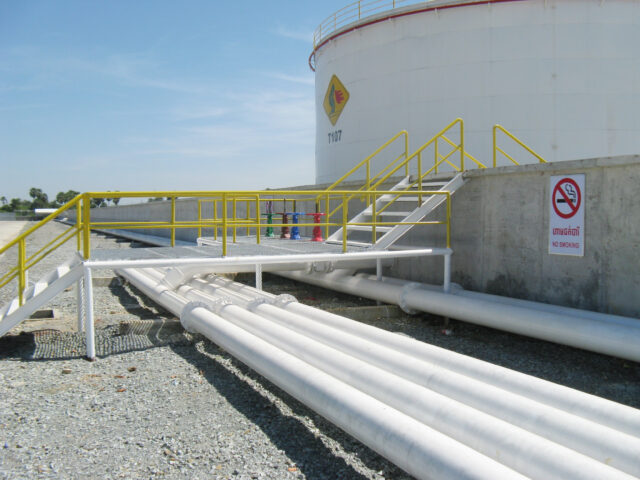